Artificial Intelligence
& Machine Learning
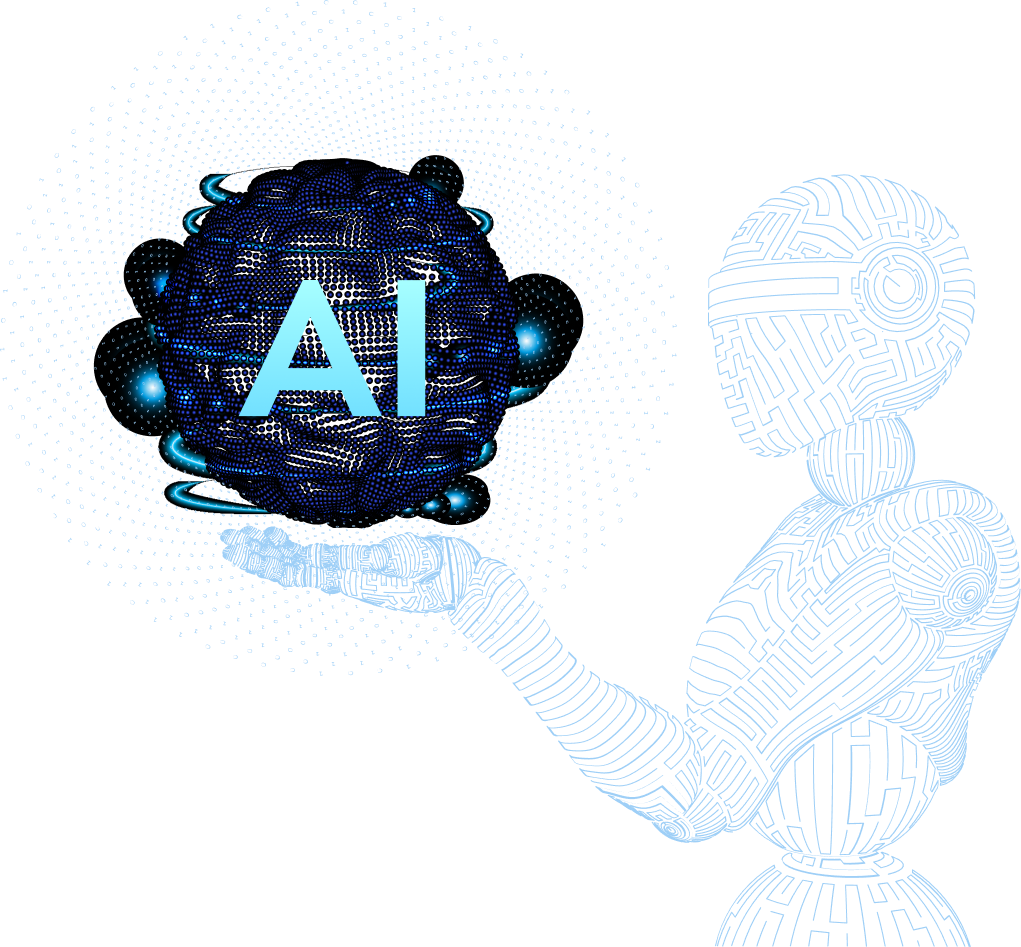
AI & ML
Client Background
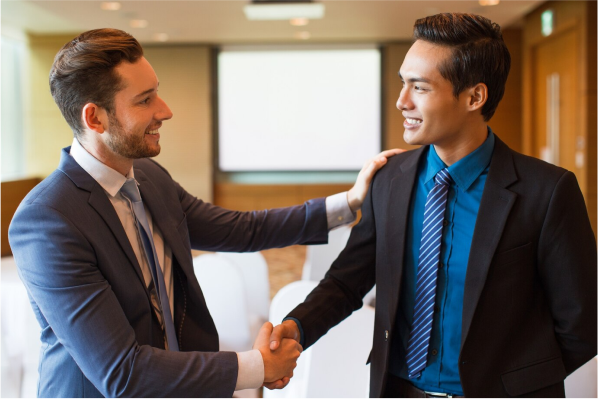
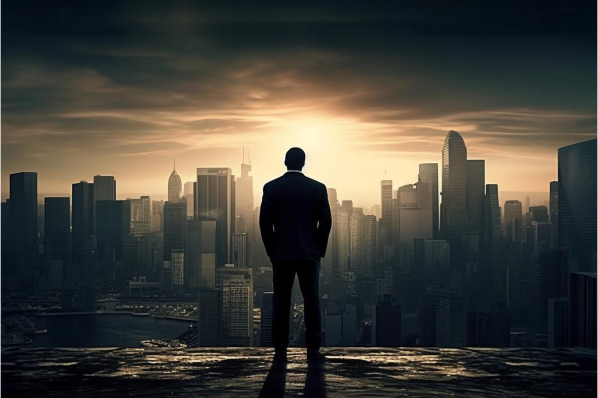
Challenge
Key challenges included
- High downtime costs due to equipment failures
- Excessive spending on preventive maintenance with limited accuracy
- Need for a predictive approach to optimize asset usage and improve productivity
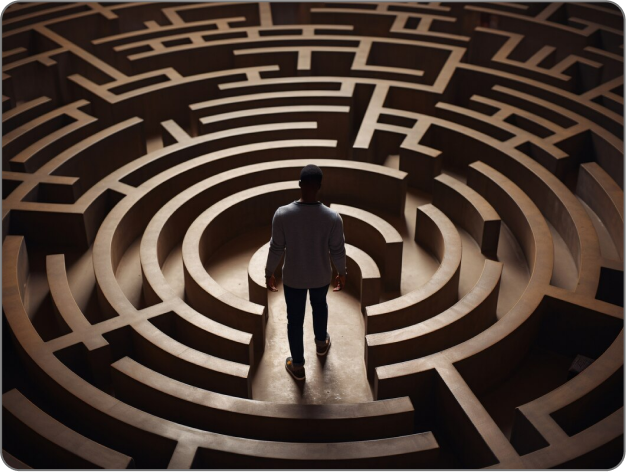
Solution
OctoElite implemented an AI-powered Predictive Maintenance System to monitor, analyze, and predict equipment health. Here’s a breakdown of our approach

Data Collection and Preparation
- We collected historical data from the client’s machinery, including sensor data (temperature, vibration, pressure), maintenance logs, and operational data.
- Data preprocessing and cleaning were essential to ensure high-quality input, as noisy or inconsistent data could impact model accuracy.

Feature Engineering & Model Development
- After analyzing data trends, we identified key features that correlated with equipment failure.
- Our data scientists developed and trained multiple machine learning models (including Random Forest, Gradient Boosting, and Neural Networks) to predict when specific parts were likely to fail.
- The model was fine-tuned based on the client’s operational requirements, achieving an accuracy rate of over 90%.

Real-time Monitoring and Predictive Alerts
- The AI models were integrated with the client’s IoT system, enabling real-time monitoring of all machinery.
- Predictive maintenance alerts were set up, notifying maintenance teams of potential failures before they happened, allowing for targeted maintenance rather than scheduled downtime.

Dashboard and Visualization
- We provided the client with an easy-to-use dashboard to visualize machine health, predictive alerts, and maintenance recommendations.
- - The dashboard provided real-time insights and visual analytics to help the team understand equipment health and optimize production.

Continuous Model Improvement
- Machine learning models improve over time with new data. We set up a feedback loop to retrain and refine the models continuously, ensuring accuracy as operational conditions changed.
Results
measurable results within the first few months of deployment:

Reduction in Downtime
The AI system successfully predicted equipment failures ahead of time, allowing for preemptive maintenance and significantly reducing unplanned downtime.

Decrease in Maintenance Costs
By avoiding unnecessary preventive maintenance and focusing on actual needs, the client saw a substantial reduction in maintenance expenses.

Increase in Equipment Lifespan
The optimized maintenance schedule led to reduced wear and tear, extending the life of critical machinery components.

Improved Production Efficiency
With fewer disruptions, the manufacturing line was able to operate at peak efficiency, increasing output and meeting production goals.
Conclusion
OctoElite’s AI-powered Predictive Maintenance Solution enabled the client to move from reactive and preventive maintenance to a predictive approach, transforming their maintenance operations and driving significant cost savings. By leveraging AI, the client achieved a more efficient, reliable, and cost-effective maintenance strategy, creating a competitive edge in the manufacturing industry.
This case study highlights how AI solutions can deliver real-world value, and OctoElite is committed to helping businesses across industries unlock the potential of AI to solve complex operational challenges.
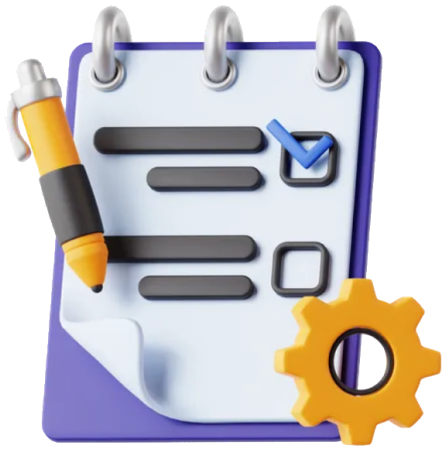
Key Takeaways
Industry
Manufacturing
Challenge
Reduce unplanned downtime and optimize maintenance
Solution
AI-powered Predictive Maintenance using real-time data and machine learning
Outcome
30% reduction in downtime, 25% cost savings, and improved equipment lifespan
This case study demonstrates the impact of AI in predictive maintenance, a versatile solution applicable to various sectors including manufacturing, energy, and transportation.
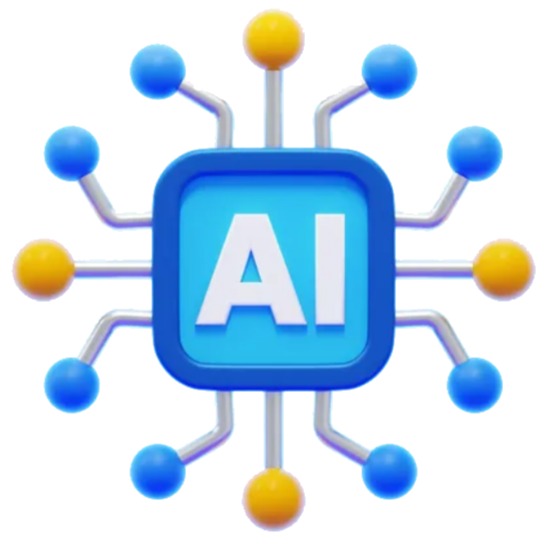